ENGINEERING SERVICES AND CONSULTING Srl
Industrial products: dot matrix impact
printhead
Needle
printheads are used in impact printers and consist of a series of
high performance electromagnets each of which actuates a needle
(diameter 0.2-0.25 mm) to hit the paper to be printed.
A ribbon made of inked fabric is placed between the needle and the
paper, which transfers the ink to the paper. The printed character
consists of a series of dots arranged following a predefined
matrix: hence the definition "dot matrix" used for this kind of
printer.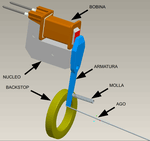
After the definition of the specifications for the industrial
product with the customer, we elaborated the concept from a
systems-based point of view, defining the main characteristics and
design constraints; we then carried out electromagnetic
simulations and an analysis of the problem using the TRIZ method.
Here you will
find the characteristics of the needle printhead we designed.
Electromagnetic simulations
With the support of the
Polytechnic University of Turin, simulation was carried out using
the finite element method (fem) to define the best design of the
electromagnet group in order to obtain the required performance.
Current absorption and energy dispersion in the form of heat have
been minimized and the impact force of the needle (rotation torque
of the armature) has been maximized.
The use of numerical simulation allowed to correctly design the
electromagnet assembly avoiding the realization of prototypes for
verification and consequently reducing time and costs of the
product development process.
TRIZ analysis..
With the support of the University of
Florence, an analysis was carried out using the TRIZ OTSM method
with the aim of maximizing print quality.
Among the various working parameters of the printhead that affect
print quality, the two emerging parameters were chosen: static
travel and impact force.
After capturing the project team's know-how in the Problem Flow
Network (diagram illustrating the network of problems and their
relationships) and conducting a detailed patent analysis, the
problems to be tackled and solved were chosen using the matrix in
the figure.
Using the tools of the TRIZ OTSM method (clouds of
contradictions, functional analysis,...), the chosen problems were
addressed and conceptual solutions defined.
The use of the TRIZ method has led to clear and quantifiable
positive effects both on the industrial product (performance,
costs, competitive factors) and on the product development process
(time and costs).
Executive design.
Starting from the results obtained with
numerical simulation and TRIZ analysis, we started the cad/cam
design phase using the parametric software PTC Creo.
The design phase has been integrated with the use of other
methodologies to support the process: DfMA (design for
manufacturing and assembly), DoE (design of experiment), DTC
(Design To Cost) and Robust Design - Taguchi.
With the 3D cad models and their associated drawings, the
technological prototypes were manufactured, assembled and tested
in order to improve and optimize the overall project.
The final cad documentation was completed with the parts list,
drawings, assembly and testing procedures and then we moved on to
mass production.
We made the special
automatic machines necessary for manufacturing and testing
and designed and set up the manufacturing workshop.
Interested in design supported by
the TRIZ method? Contact us we will be glad to provide
you with all the information you need.
Download our TRIZ
paper: An effective product development TRIZ based approach
and the Application
of the TRIZ method to design - case study
Copyright 2007-2017 - ESC Engineering Services and
Consulting Srl - P. IVA 09705560010
Privacy Policy